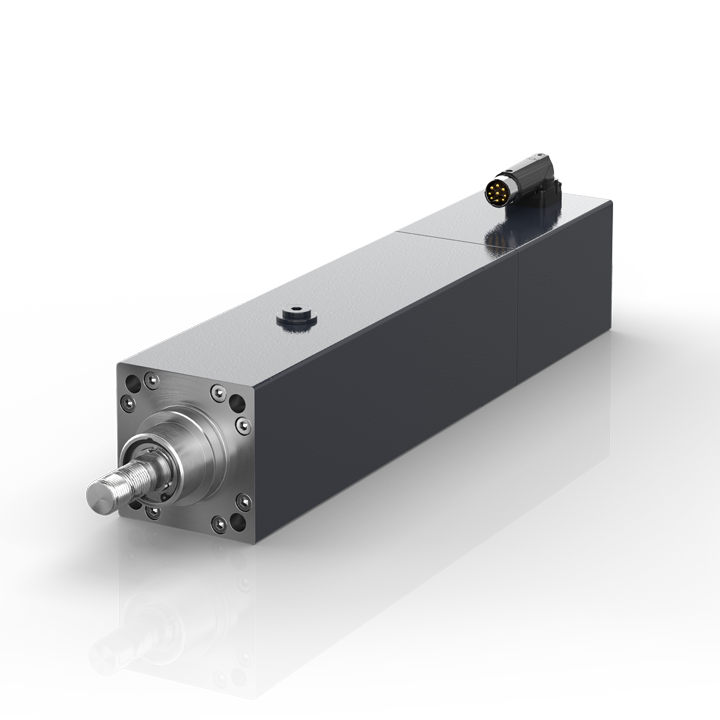
The electric cylinders from the AA3000 series are the ideal direct drives for linear applications with high process forces and speeds. The advantages with regard to force, dynamics and compactness meet the advantages of servo technology such as controlled positioning, safe holding at a standstill and high efficiency. The integrated mechanism of precise roller bearings, ball screw and guide provides for a backlash-free, purely translatory motion.
At the shaft end of the spindle is an external thread on which conventional adapters such as ball heads or clamping hooks from the pneumatic/hydraulic range can be mounted. The flange size of the electric cylinder is based on ISO 15552 and has bolting points on both sides in case, for example, an application requires a swivel bolt connection. This compatibility makes the conversion from pneumatic to electric drive technology particularly easy.
In addition to the high resolution, the safe 24-bit multi-turn encoder installed offers the advantages of OCT and electronic nameplate for fast and simple commissioning with the familiar Drive Manager. Other spindle pitches or a backlash-free holding brake are available as options.
Highlights
- based on the proven AM8000 drive technology
- compact dimensions thanks to fully integrated mechanism
- simple conversion of pneumatic applications due to compatibility with ISO 15552
- combines the force, dynamics and compactness of pneumatics with the controllability and efficiency of an electric servo drive
Product status:
regular delivery
Product variants | Peak force | Continuous force | Max. speed | Max. acceleration |
---|---|---|---|---|
AA3033-2xyz | 12,500 N | 3700 N | 0.50 m/s | 10 m/s² |
AA3033-4xyz | 6250 N | 1850 N | 1.0 m/s | 20 m/s² |
Product information
Technical data | AA3033-4xyz |
---|---|
Motor type | permanent magnet-excited three-phase synchronous motor with integrated spindle drive |
Nominal voltage | 100…480 V AC |
Peak force | 6250 N |
Continuous force | 1850 N |
Peak current | 15 A |
Continuous current | 4.7 A |
Max. speed | 1.0 m/s |
Max. acceleration | 20 m/s² |
Max. stroke | 200 mm |
Spindle pitch | 10 mm with anti-twist protection |
Cooling | convection |
Motor feedback | OCT, 24 bit, SIL 2-capable, multi-turn absolute encoder |
Connection method | itec® plug |
Ambient temperature (operation) | +5…+40°C |
Approvals/markings | CE |
All electric quantities are RMS values.
Housing data | AA3xxx |
---|---|
Protection rating | IP50, IP54 with venting hose instead of venting plug |
Design form | flange according to ISO 15552, flange-mounted according to IM B14, IM V18, IM V19 |
Material | aluminum |
Coating/surface | dark gray powder coating, similar to RAL7016 |

Dimensions | AA3033-4xyz |
---|---|
a | 45 f8 |
b | M16 x 1.5 |
d | 32 mm |
l | 56.5 mm |
r | 75 mm |
k | 380 mm (Order option z (holding brake) has no influence on the overall length ot the motor) |
Order reference
AA3033-4xyz | |
---|---|
x = 3 | 200 mm stroke |
y = H | One Cable Technology for power and feedback: feedback transmission via motor cable, no feedback cable necessary, electronic identification plate, multi-turn, absolute position within 4096 revolutions, resolution 24 bit, SIL 2-capable |
z = 0 | without holding brake |
z = 1 | with permanent magnet-excited holding brake |
The options cannot be installed in the field. |
Loading content ...
Loading content ...
© Beckhoff Automation 2024 - Terms of Use