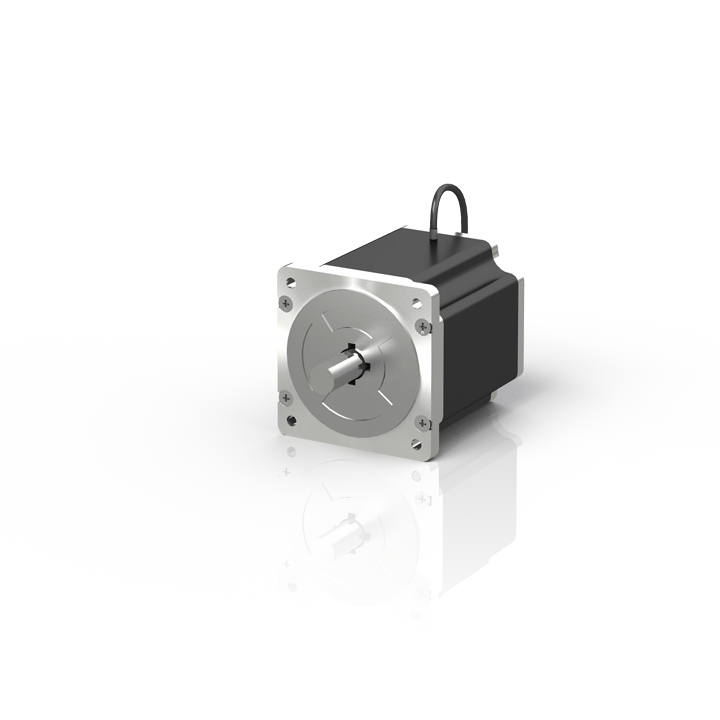
The AS1000 stepper motors with flange codes from 42 to 86 mm (N1 = NEMA17, N2 = NEMA23, N3 = NEMA34) and torques from 0.4 to 5 Nm are ideally suited for use as auxiliary axes and positioning drives. They are characterized by robustness and high holding torques. Due to the integrated micro-stepping the motors can position very well even without a feedback system and require only a motion terminal for power electronics. Stepper motors can also be operated with TwinCAT NC PTP for synchronization functions such as cam plates or flying saws.
Product status:
regular delivery (not recommended for new projects) | recommended alternative: AS2042
Product information
Data for 48 V DC | AS1060 |
---|---|
Nominal voltage | 24…48 V DC |
Holding torque | 5.00 Nm |
Rated current | 5.0 A |
Resolution | 1.8°/200 full steps |
Connection method | M12 cable bundle |
Ambient temperature (operation) | 0…+40°C |
Approvals/markings | CE |
Housing data | AS106x |
---|---|
Protection rating | IP20 |
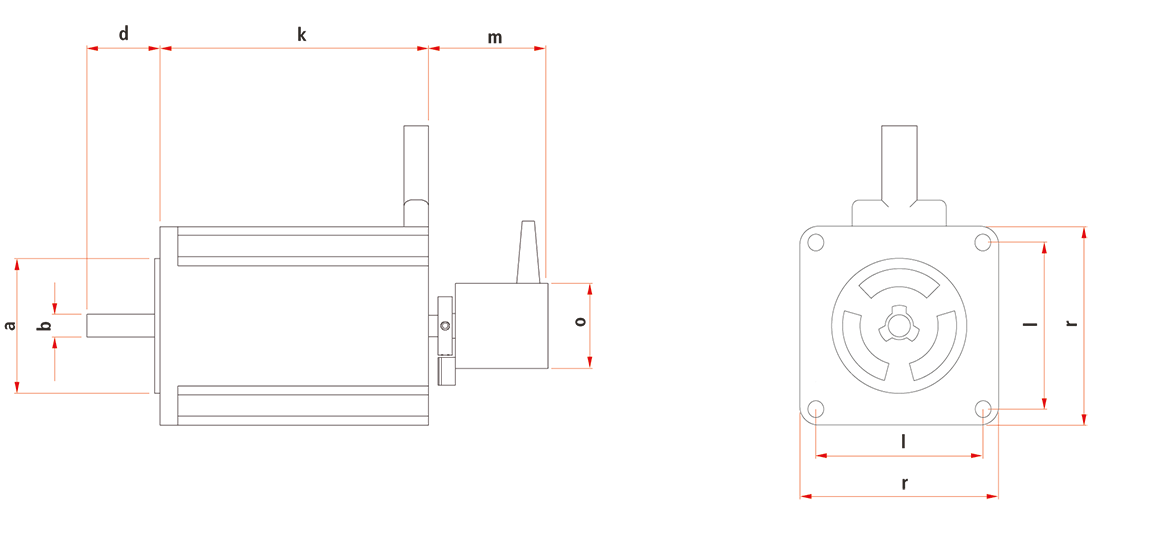
Dimensions | AS1060 |
---|---|
a | 73 mm |
b | 14 mm |
d | 30 mm |
k | 96.5 mm |
l | 69.6 mm |
m | 33 mm |
o | 24 mm |
r | 85.5 mm (NEMA34) |
Order reference
AS1060-wxyz | |
---|---|
w = 0 | smooth shaft with 2 flats |
w = 1 | shaft with groove and feather key according to DIN 6885 (only available with AS1060) |
x = 0 | standard motor without second shaft |
x = 1 | second shaft (for AS1020/AS1050/AS1060 only), necessary for encoder |
y = 0 | no incremental encoder |
y = 1 | incremental encoder, 24 V DC, 200 increments (only available for AS1020, AS1050, AS1060), requires x = 1 |
y = 2 | incremental encoder, 24 V DC, 1024 increments (only available for AS1020, AS1050, AS1060), requires x = 1 |
z = 0 | standard |
Loading content ...
Loading content ...
Loading content ...
Loading content ...
© Beckhoff Automation 2025 - Terms of Use