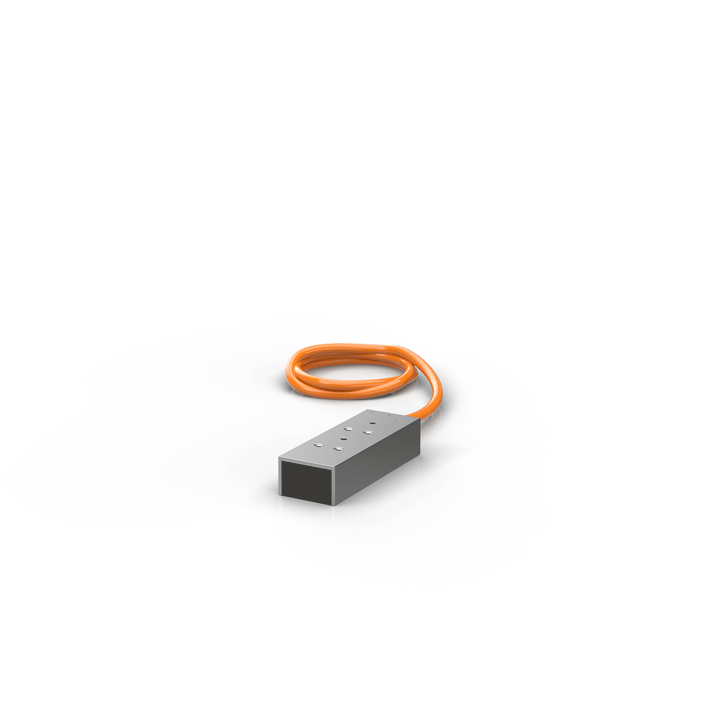
The AL8121 linear servomotor is suitable for highly dynamic and powerful linear axes operating on 48 V DC and has a pole pair distance of 24 mm. The optimized product design and modular coil concept allow for maximum force density within a minimal footprint. The overall length of the primary part is 93 mm. The AL8121 reaches a maximum speed of 2.5 to 4.5 m/s with a peak force Fmax of 100 N. Cooling is achieved via convection.
Symmetrical and flexible motor design
The AL8100 linear motors feature a symmetrical drilling pattern that simplifies the design and allows for a universal machine configuration. In addition, critical hotspots are avoided by allowing for even contact between the linear motor and the machine carriage.
High force density
The modular coil concept allows for a flexible and highly compact design of the linear motor. Despite this compact design, the space-saving linear motors in the AL8100 series feature high peak forces and thus provide optimum force density.
Made in Germany
Both the development and the production of the AL8100 take place in Germany. With its long-standing experience in drive technology, Beckhoff guarantees a high level of product quality for durable and reliable applications.
One Cable Technology
The primary parts can be optionally equipped with One Cable Techonolgy (OCT). In this setup, the scanning head of the linear encoder forms a unit together with the primary part, both mechanically and electrically. This means that only one cable is required for the power supply, feedback system, and thermal sensor. In addition to the reduced cabling effort and the associated faster electrical installation, commissioning is also simplified by an online assessment rating of the encoder’s signal quality and the electronic nameplate. When connected to the ELM72xx servo terminals, all relevant motor parameters are read out directly. What’s more, the mechanical assembly of the scanning head is not required, since this is achieved by installing the primary part.
The complete system requires additional components, such as the scale tape and the rail for simplified installation of the scale tape.
Product status:
regular delivery | estimated market release of the OCT version on request
Product information
Data for 24 V AC | AL8121-0Eyz-0000 |
---|---|
Motor type | 3-phase synchronous linear servomotors |
Nominal voltage | 24…48 V DC |
Max. speed | 2.5 m/s |
Peak force | 100 N |
Continuous force | 56 N |
Peak current | 5.6 A |
Continuous current | 2.8 A |
Force constant | 20 N/A |
Cooling | convection |
Connection technology | itec® plug |
Ambient temperature (operation) | 5…40°C |
Approvals/markings | CE, cURus, EAC |
Housing data | AL80xx | W2 |
---|---|
Protection rating | IP64 |
Overall width | W2 (50 mm) |
Material | aluminum |

Dimensions | AL8121-0Eyz-0000 |
---|---|
b | 51 mm |
la | 93 mm |
h | 40 mm |
- Continuous operation @ 24 V DC
- Continuous operation @ 48 V DC
- Voltage boundary curve @ 24 V DC
- Voltage boundary curve @ 48 V DC
Order reference
AL8121-wxyz-0000 | |
---|---|
w = 0 | convection cooling |
x | winding code A…Z |
y = 0 | without feedback |
y = 1 | One Cable Technology for power and feedback: feedback transmission via motor cable, no feedback cable necessary, inductive scanning head, absolute position, 0.1 µm resolution, product announcement | estimated market release on request |
z = 0 | 1.00 m connection cable with wire end ferrules |
z = 1 | 0.50 m connection cable with plug |
All electric quantities are RMS values. | |
The options cannot be installed in the field. |
Loading content ...
Loading content ...
© Beckhoff Automation 2025 - Terms of Use