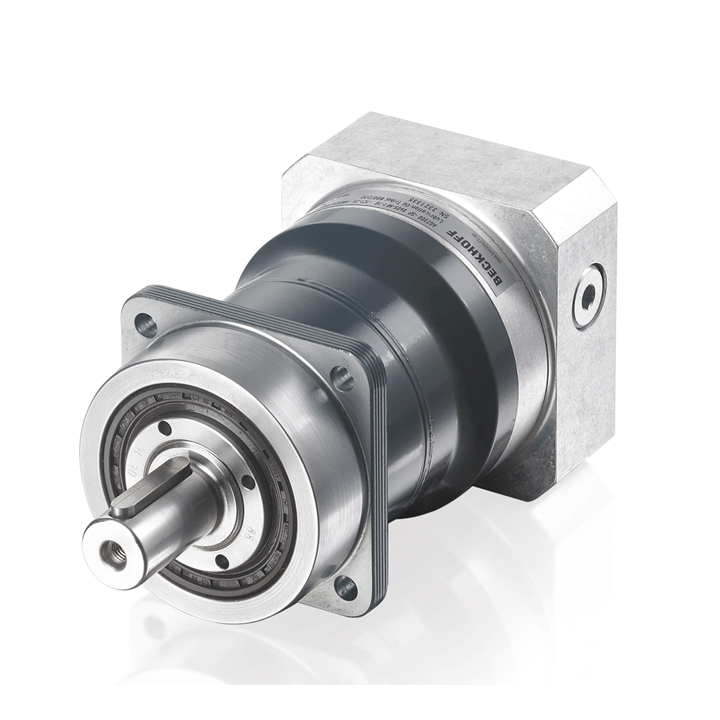
The low-backlash, high-performance planetary gear units of the AG2300 series offer high torque, low torsional backlash and a very low noise level in various gear ratios. The high-end gear units for the rotary servomotors have a high power density and are able to absorb high radial and axial forces. The high quality and running smoothness of this helical gear unit series meet the highest control quality demands.
The MF standard variant allows high positioning accuracy and highly dynamic operating cycles (duty cycle < 60%). The high-speed MC variant is suited for positioning with high nominal speeds in continuous operation (duty cycle > 60%).
The gear units of the AG2300 series are perfectly matched to rotary servomotors. The inertia ratios, the required torques and the suitable motors can be conveniently calculated directly in TwinCAT with the TwinCAT 3 Motion Designer. In addition, the tool checks in a single step whether the selected motor can be adapted to the gear unit. The planetary gear units are fitted to the respective motor in the factory and delivered as a complete motor/gear unit.
Features
- equipped with output shaft
- standard version MF for high positioning quality in highly dynamic operating cycles, high-speed version MC for high speeds in continuous operation
- available in 7 or 6 sizes
- MF: SP060 to SP240
- MC: SP075 to SP240
- acceleration torques between 36 and 5400 Nm
- high axial and radial forces
- maximum efficiency, maximum power density
- low torsional backlash
- low running noise and smooth running thanks to helical gearing
- lubricated for life
- IP65 protection rating; any installation position
- integrated into TwinCAT 3 Motion Designer for optimal specification
Product status:
regular delivery
Product information
Technical data | AG2300-+SP240S-MF2-16 |
---|---|
Design | straight |
Variant | high-end |
Version | standard MF |
Nominal output torque | 2658 Nm |
Max. acceleration torque | 5400 Nm |
Gear stages | 2 |
Gear ratio | 16 |
Max. torsional backlash standard/reduced | ≤ 5/3 arcmin |
Ambient temperature (operation) | -15…+40°C |
Housing data | AG2300 |
---|---|
Protection rating | IP65 |
Design form | flange-mounted according to B5 |
Coating/surface | anodized, heat-treated steel |
Order reference | AG2300-+SPaaaS-MFs-i-wXy-Motorsize |
---|---|
aaa | series/size (060, 075, 100, 140, 180, 210, 240) |
s = 1 | 1-stage with i = 3/4/5/7/10 |
s = 2 | 2-stage with i = 16/20/25/28/35/40/50/70/100 |
i | gear ratio |
w = 0 | smooth shaft |
w = 1 | shaft with groove and feather key according to DIN 6885 |
y = 0 | reduced torsional backlash |
y = 1 | standard torsional backlash |
X | identifying letter for clamping hub diameter; not available for selection, is selected automatically based on the respective motor |
Motorsize | Specifies adapter unit between motor and gearbox. Correlates to motor flange code F or flange compatible motor type. |
Motorsize = F1 | flange code F1: AM801x, AM811x |
Motorsize = F2 | flange code F2: AM802x, AM812x, AMI812x |
Motorsize = F3 | flange code F3: AM803x, AM813x, AM853x, AMI813x, AMP803x, AMP853x |
Motorsize = F4 | flange code F4: AM804x, AM814x, AM854x, AMP804x, AMP854x |
Motorsize = F5 | flange code F5: AM805x, AM855x, AMP805x, AMP855 |
Motorsize = F6 | flange code F6: AM806x, AM856x |
Motorsize = F7 | flange code F7: AM807x |
Loading content ...
Loading content ...
© Beckhoff Automation 2024 - Terms of Use