The compact AX8000 multi-axis system
The compact AX8000 multi-axis system enables high-precision positioning and machining processes in extremely short control cycles. Already integrated: TwinSAFE Logic with 16 drive-integrated safety functions.
More about this video

Motion
Our innovative drive technologies give you almost unlimited capabilities when it comes to realizing your application.

Servo drives
Compact stand-alone, double-axis or multi-axis servo drives for any application – TwinSAFE and multi-feedback interface are optionally selectable.

AX8000 | Multi-axis servo system
The AX8000 is the space-saving solution for applications with more than two axes. Extensive TwinSAFE functions allow a safe machine design.
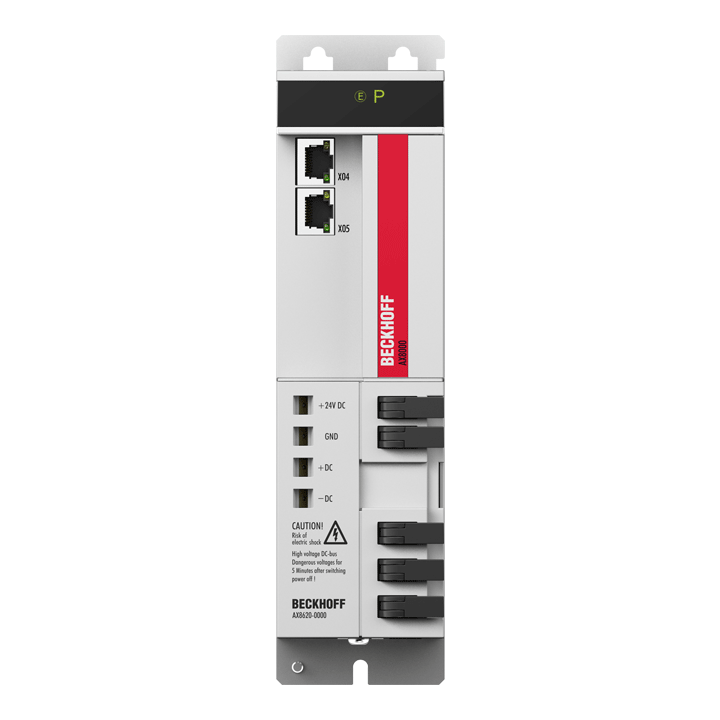
AX8620 | Power supply module
A power supply module generates the DC link voltage (DC) for the power supply of the axis modules and the option modules from the mains voltage. It already contains a mains filter, for which the drive is tested and certified in accordance with EN 61800-3 for Category C3 use.
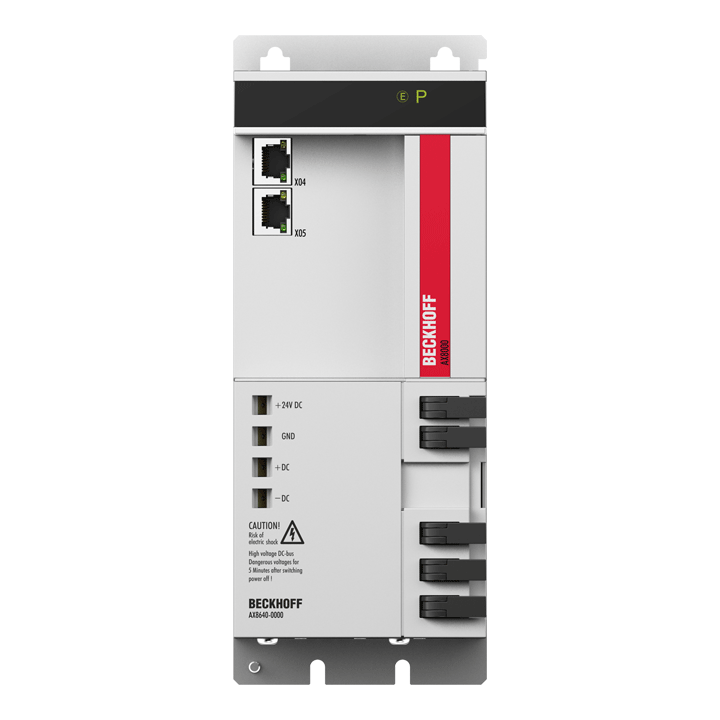
AX8640 | Power supply module
A power supply module generates the DC link voltage (DC) for the power supply of the axis modules and the option modules from the mains voltage. It already contains a mains filter, for which the drive is tested and certified in accordance with EN 61800-3 for Category C3 use.
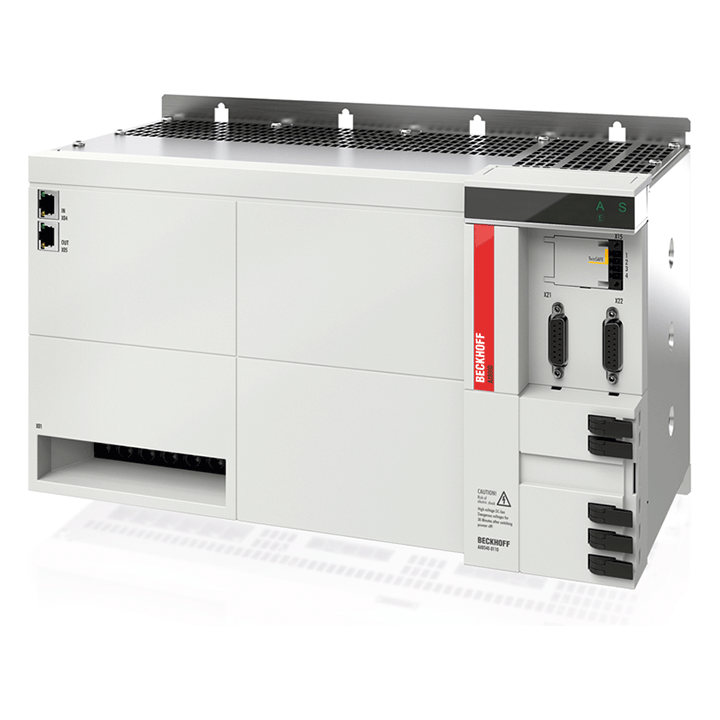
AX8525 | Combined power supply and axis module
The AX8525 and AX8540 combined power supply and axis modules unite the function of an AX86xx power supply module with an AX81xx axis module in a single device. As a result, the AX-Bridge is not loaded by the axis current of the first axis and up to 50 A DC are available for additional axis modules. The power supply provides 80 A DC to the DC link and contains an internal brake resistor as well as a chopper for the connection of an external brake resistor. The integrated axis module with TwinSAFE safety functions is available with a rated current of 25 A or 40 A and can optionally be ordered with multi-feedback interface.
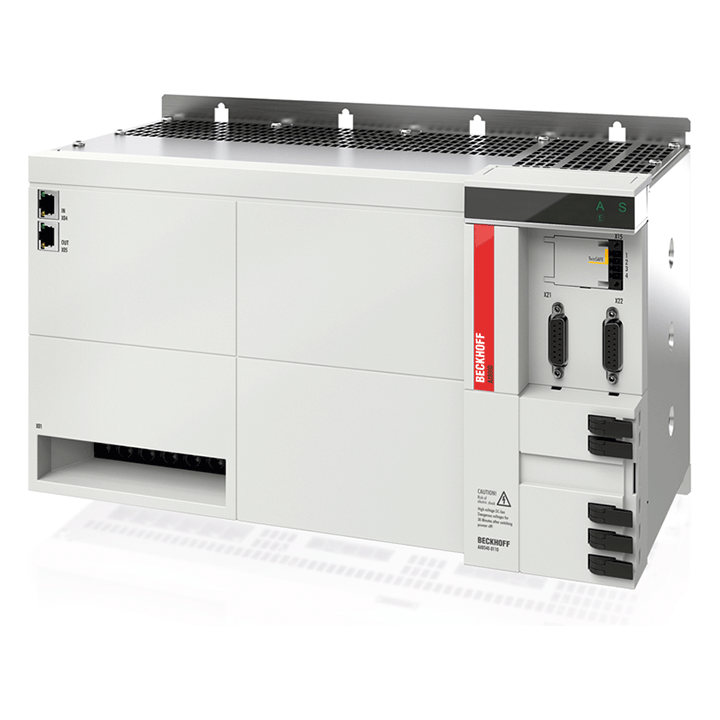
AX8540 | Combined power supply and axis module
The AX8525 and AX8540 combined power supply and axis modules unite the function of an AX86xx power supply module with an AX81xx axis module in a single device. As a result, the AX-Bridge is not loaded by the axis current of the first axis and up to 50 A DC are available for additional axis modules. The power supply provides 80 A DC to the DC link and contains an internal brake resistor as well as a chopper for the connection of an external brake resistor. The integrated axis module with TwinSAFE safety functions is available with a rated current of 25 A or 40 A and can optionally be ordered with multi-feedback interface.
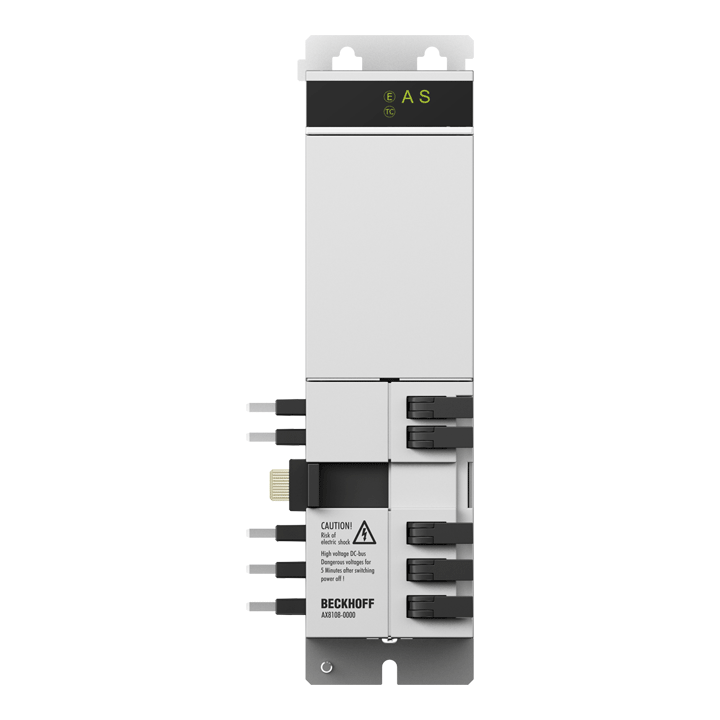
AX8108 | Single-axis module
An axis module contains the DC link and the inverter for supplying the motor. Depending on the required number of axes, the axis modules are attached to the power supply module to form the multi-axis servo system. Axis modules with different ratings can be combined in order to enable an optimized design of the individual axes.

AX8118 | Single-axis module
An axis module contains the DC link and the inverter for supplying the motor. Depending on the required number of axes, the axis modules are attached to the power supply module to form the multi-axis servo system. Axis modules with different ratings can be combined in order to enable an optimized design of the individual axes.
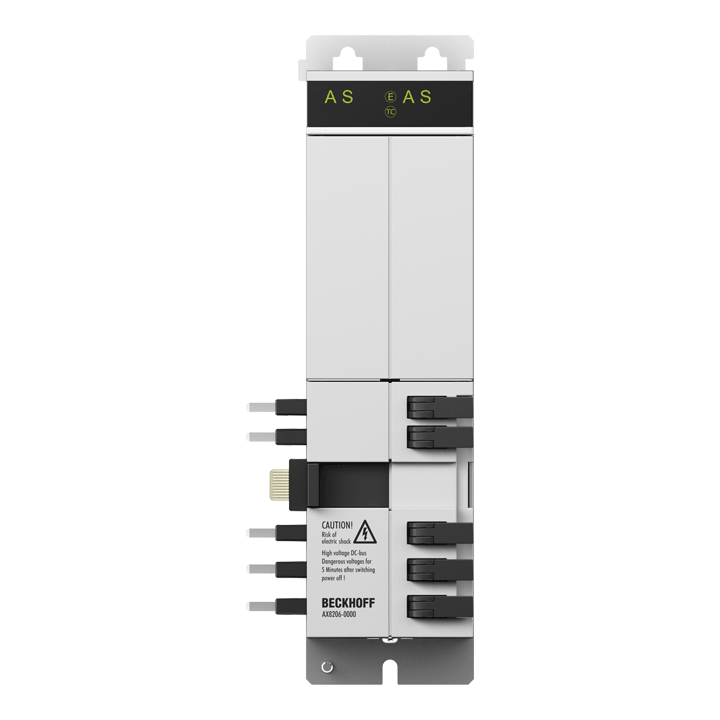
AX8206 | Dual-axis module
An axis module contains the DC link and the inverter for supplying the motor. Depending on the required number of axes, the axis modules are attached to the power supply module to form the multi-axis servo system. Axis modules with different ratings can be combined in order to enable an optimized design of the individual axes.
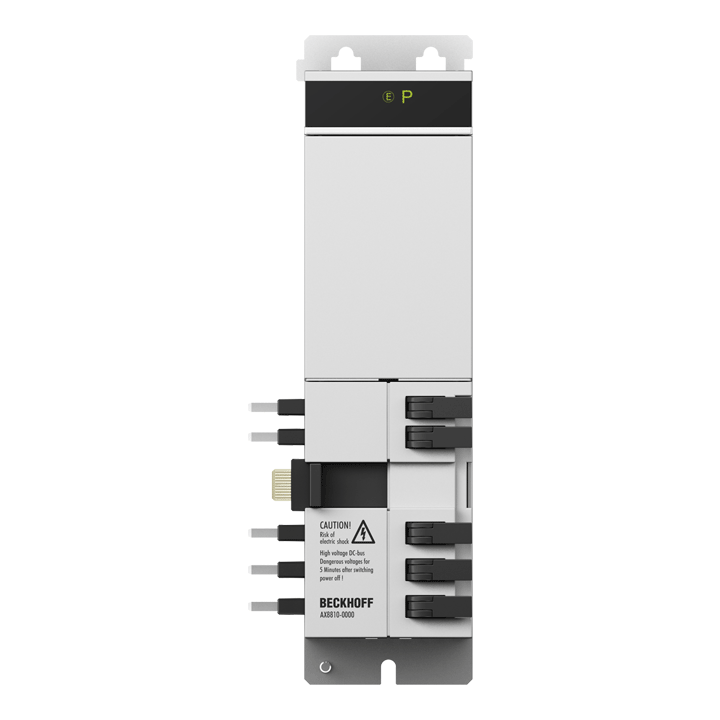
AX8810 | Capacitor module
An AX8810 capacitor module extends the DC link capacitance and is suitable for the support of the DC link. It enables energy savings: voltage peaks generated by braking motors are taken up and stored. This makes the activation of the brake resistor mostly unnecessary and helps to reduce power losses. Overall, the use of the capacitor module makes a reduction in the total connected load possible and also a smaller dimensioning of the fuse.
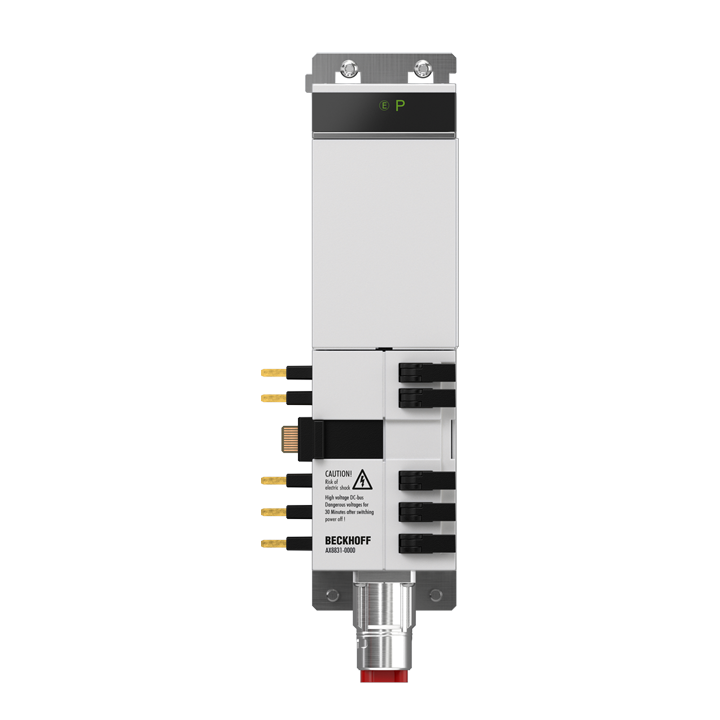
AX8831 | AMP8000 coupling module for AX8000
For connecting AMP8000 distributed Servo Drives to the PC-based control technology, and more specifically to the EtherCAT-based Servo Drive systems there are two coupling modules available in single-channel and dual-channel versions. The coupling modules provide a connection for the DC link intermediate circuit, 24 V DC power supply and EtherCAT communication. Distributed servo drives can be coupled to the AX8000 multi-axis servo system via an AX883x power supply module. By means of the 1- or 2-channel coupling modules and the AMP8805 distribution module, the implementation of simple as well as complex distributed drive solutions is easy and straightforward.
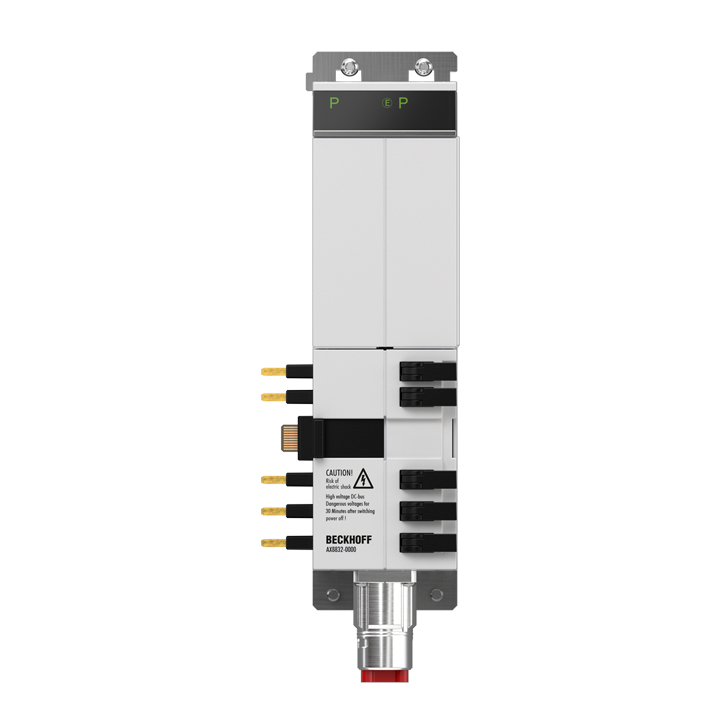
AX8832 | AMP8000 coupling module for AX8000
For connecting AMP8000 distributed Servo Drives to the PC-based control technology, and more specifically to the EtherCAT-based Servo Drive systems there are two coupling modules available in single-channel and dual-channel versions. The coupling modules provide a connection for the DC link intermediate circuit, 24 V DC power supply and EtherCAT communication. Distributed servo drives can be coupled to the AX8000 multi-axis servo system via an AX883x power supply module. By means of the 1- or 2-channel coupling modules and the AMP8805 distribution module, the implementation of simple as well as complex distributed drive solutions is easy and straightforward.

Entertainment industry
Ultimate guest experience: PC-based control for the entertainment industry

Sheet metal working
High performance built-in: PC-based control from Beckhoff for all control and drive applications in sheet metal working

Machine tools
Scalability and high performance: The integrated software CNC solution from Beckhoff increases the productivity of machine tools.

Plastics machines
PC-based control from Beckhoff offers integrated control systems for all manufacturing processes in the plastics industry.

Woodworking machines
PC-based control from Beckhoff provides a competitive edge in the woodworking industry by optimizing transport and handling along with edge, CNC and surface processing.

Tire and rubber industry
Leading the way in the rubber and tire industry: PC-based control technology from Beckhoff optimizes the production process.

Window production machines
PC-based control solutions from Beckhoff increase the efficiency and performance of window production machines and also simplify engineering.

Handling and assembly technology
PC-based control technology from Beckhoff optimizes the entire process chain: from handling, production, and assembly to testing, control, and management.