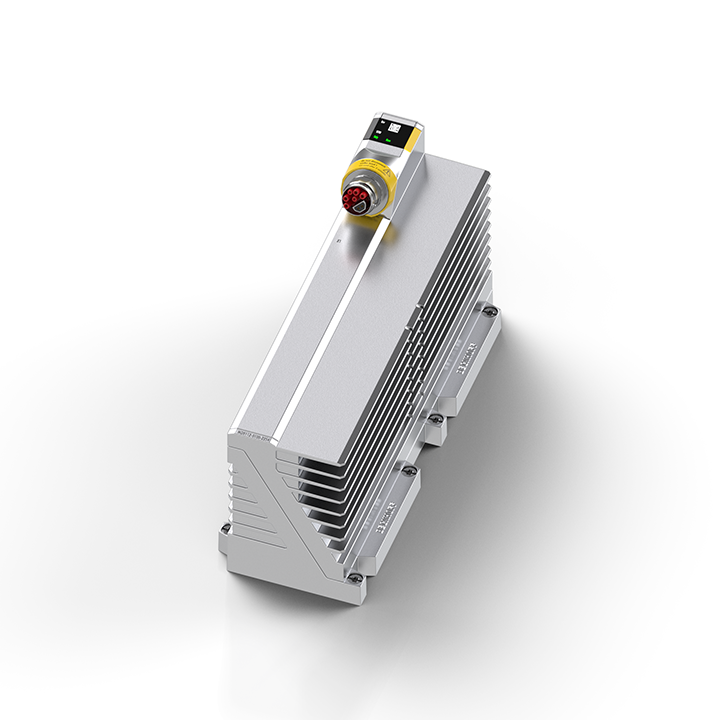
The MD8xxx series servo drives enable the operation of servomotors in the MX-System and are part of a multi-axis system whose DC link is fed from a DC link module (MD6xxx). The motor is connected via a B17 hybrid connector, which includes OCT feedback and brake control.
In addition, the servo drives have integrated STO/SS1 functionality and TwinSAFE Logic. Full TwinSAFE Safe Motion functionality is available as an option.
Product status:
product announcement | estimated market release 1st quarter 2025
Product information
Technical data | MD8112-0100-2254 |
---|---|
Product category | drive modules |
Category/version | servo drives |
DC link voltage | max. 848 V DC |
Channels | 1 |
Output current | 12 A |
Peak current | 24 A |
Motor connection | B17 connector |
Feedback | OCT |
Safety functions | STO, SS1, integrated TwinSAFE logic |
Housing data | R2S2T3 KR27 |
---|---|
Baseplate interface | data connector (1-row) |
Number of slots | 1 |
Operating temperature | 0…50°C |
Storage temperature | -25…85°C |
Protection rating | IP65/67 |
Approvals/markings | CE, UL (in preparation) |
Loading content ...
© Beckhoff Automation 2024 - Terms of Use