
An alternative operating system – TwinCAT/BSD – will be available for selected Beckhoff Industrial PC platforms. TwinCAT/BSD combines the TwinCAT runtime with FreeBSD®, an industrially tested and reliable open source operating system.
For many years, Windows CE was the basic operating system for all Beckhoff Industrial PCs. With the foreseeable end of Windows CE, Beckhoff is presenting at an early stage a successor that combines the advantages of Windows CE – inexpensive use on all platforms – with the advantages of the large Windows systems. In addition to a successor to Windows CE, Beckhoff thus also offers an alternative to Windows 7 and Windows 10.
What is FreeBSD®?
FreeBSD® is a UNIX®-compatible open source operating system directly originating from Berkeley Software Distribution (BSD). As an open source project, FreeBSD® is continually being developed further, improved and optimized by a large group of developers. On account of the BSD license Beckhoff has opted for FreeBSD®, which enables the integration of TwinCAT without licensing problems.
FreeBSD® supports both 32- and 64-bit platforms and makes scalable systems possible with Arm® CPUs extending up to powerful Intel® Xeon® CPUs.
Further information on FreeBSD® can be found on the homepage of the FreeBSD Foundation or that of the FreeBSD® project:
https://www.freebsdfoundation.org
https://www.freebsd.org
TwinCAT
TwinCAT/BSD supports all TwinCAT 3 runtime functions. The programming is still carried out with the familiar Visual Studio-based TwinCAT 3 XAE from a Windows development computer. TwinCAT/BSD offers multi-core support, allowing individual cores to also be reserved for the exclusive use of TwinCAT.
In addition to the TwinCAT HMI Server, a modern HTML5 web browser can be used as a client for TwinCAT HMI. The configuration takes place as usual via the graphic editor of the TwinCAT 3 XAE development environment.
Software and Updates
In addition to a large number of FreeBSD® programs, TwinCAT functions can also be installed via the Beckhoff Package Server. Moreover, the uncomplicated updating of the operating system as well as the TwinCAT runtime is possible in this way via the network. Software packages can also be installed offline. The software packages are first loaded to a development computer with a network connection and later installed directly on the Beckhoff Industrial PC. The hosting of the customer's own package server on their side is also possible. Apart from FreeBSD® programs that can be offered in this way, many well-known programs from Linux® are also available.
Write filter
As is familiar from the Windows operating system, TwinCAT/BSD provides a write filter. This protects the system against persistent changes. With the write filter activated, the system is in a previously defined state following a restart.
Backup and restore
A TwinCAT/BSD system can be backed up and restored using a USB stick that offers similar functions as the Beckhoff Service Tool for Windows operating systems. A backup can also be created from the live system, which is backed up locally or via the network to a remote system.
Small footprint
The current minimum size of a basic image is around 300 MB, with a very small RAM consumption of < 100 MB. Hence, very compact controllers will also be possible in future with TwinCAT/BSD.
Device Manager
The already well-known IPC Device Manager is also used for the configuration of the system under TwinCAT/BSD. This can be done via website or also under program control via the familiar ADS Secure or OPC UA interfaces.

Container and virtualization
On account of its FreeBSD® basis, TwinCAT/BSD also includes the well-known container technology Jails as standard. Jails have been part of FreeBSD® since the year 2000 and are thus long since proven and stable. In addition, it is also possible to use Docker® containers by means of virtualization. For this purpose, a Linux® VM, which serves as a Docker® host for the Docker® containers, is started in the TwinCAT/BSD Hypervisor.
The TwinCAT/BSD Hypervisor is a system feature of the TwinCAT/BSD operating system from Beckhoff and enables the simultaneous execution of virtual machines and TwinCAT real-time applications on a Beckhoff Industrial PC.
Optimized integration of the hypervisor into the TwinCAT/BSD operating system and coordination of software and Industrial PC hardware enable maximum performance of virtual machines while maintaining TwinCAT real-time properties for machine control. The TwinCAT/BSD Hypervisor benefits from the high performance and hardware-based virtualization technologies of modern Intel® and AMD CPUs in Beckhoff Industrial and Embedded PCs. The high-performance execution of virtual machines enables the strengths of different operating systems to be used on a Beckhoff Industrial PC and the security properties of the overall system to be improved by operating user environments in a modular and isolated manner.
Products
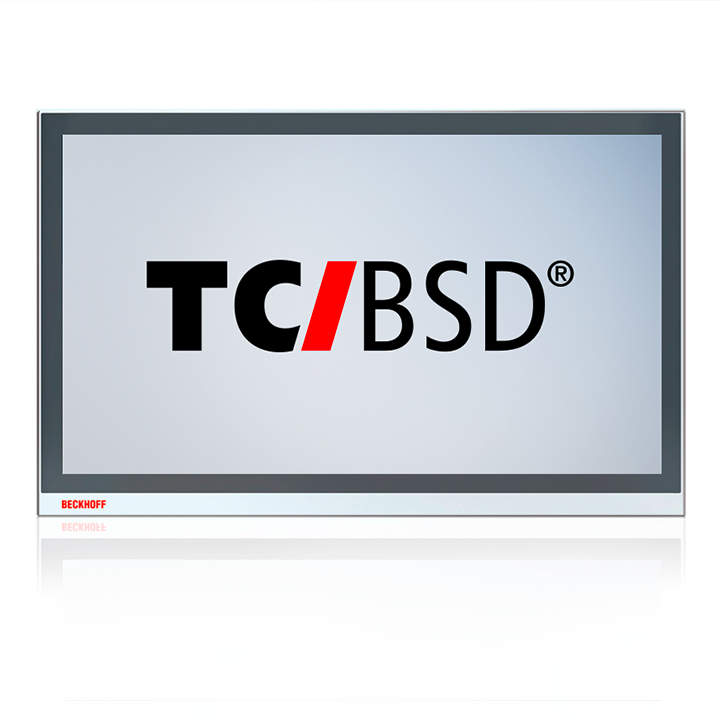
C9900-S6xx, CXxxxx-0185 | TwinCAT/BSD for Beckhoff Industrial PCs
An alternative operating system – TwinCAT/BSD – will be available for selected Beckhoff Industrial PC platforms. TwinCAT/BSD combines the TwinCAT runtime with FreeBSD®, an industrially tested and reliable open source operating system.

TwinCAT/BSD Hypervisor
Increased availability due to integrated VM environments: TwinCAT/BSD Hypervisor

IPC
We deliver Panels and Industrial PCs for every application – with the latest technology for all performance classes.

TwinCAT
The TwinCAT software system turns almost any PC-based system into a real-time control with multiple PLC, NC, CNC and/or robotics runtime systems.