

OPC Unified Architecture (UA)
Technology, products, and setting the standard in data exchange
Beckhoff has been a pioneer in open standards for many years, allowing its customers to benefit from its particularly extensive interoperability between Beckhoff and third-party products. The great commitment in the area of OPC standardization is an essential component of this. This includes the participation in numerous working groups of the OPC Foundation, the implementation of product certifications or the participation in Plugfests, the interoperability workshops, which are organized and run annually by the OPC Foundation, including in Europe. Here, the aspects provided for in the specifications are tested in practical use so that real interoperability between the OPC UA products of the participating manufacturers is increased. This commitment directly influences product development and is reflected in a wide range of products that can be used for a variety of applications.
Application scenarios of Beckhoff OPC UA products

Of course, the OPC UA client/server architecture can also be used to implement machine-to-machine scenarios – taking into account the advantages, but also, from a performance point of view, the disadvantages of the underlying TCP/IP communication connection. Publisher/subscriber mechanisms were added to the OPC UA specification in 2016, allowing communication to be routed via "message-oriented middleware". In the local network, UDP can be used as the transport channel for this purpose. When communicating across network boundaries, MQTT lends itself as a transport channel. With the TF6105 TwinCAT 3 OPC UA Pub/Sub function, Beckhoff provides the mechanisms to use both transport paths directly from real time.
Beckhoff is a member of the Field Level Communications (FLC) initiative within the OPC Foundation, which defines an open, uniform interface for control communication (OPC UA FX Controller-to-Controller). This standard describes device and configuration models that can be used to configure and establish interoperable communication relationships between machines and/or controllers from different manufacturers using OPC UA Client/Server and OPC UA Pub/Sub.

The inclusion of cloud services in the automation process is becoming increasingly attractive, whether for the implementation of central data storage or even for analysis purposes. By extending OPC UA with publisher/subscriber mechanisms, such cloud services can be connected, e.g. via the MQTT transport protocol. With the products TF6105 TwinCAT 3 OPC UA Pub/Sub and TF6720 TwinCAT 3 IoT Data Agent, Beckhoff provides two TwinCAT 3 functions to address such application scenarios. In addition, the IoT bus coupler EK9160 enables direct connection of the I/O level to the cloud via MQTT.

With the functions TE6100 TwinCAT 3 OPC UA Nodeset Editor and TF6100 TwinCAT 3 OPC UA, Beckhoff enables the integration of companion specifications into the automation project as well as their subsequent use. The Nodeset Editor can be used to load companion specifications (or the resulting nodeset files) and use them for modeling the machine project. Data points from the companion specification can be graphically linked to data points from the PLC. Automatic PLC code generation reduces the engineering effort and makes integration easier. The resulting project can then be loaded into the TwinCAT OPC UA server, providing OPC UA clients with a standardized interface for accessing machine data based on the companion specification.

The TwinCAT 3 Scope is a software oscilloscope for the graphic representation of signal curves in different chart types. These could be, for example, YT, XY, bar or digital charts. Long-term recordings, advanced export options and trigger-controlled storage are included in the range of functions. Through the integration of OPC UA, TwinCAT Scope also enables access to variables from third-party devices, allowing them to be diagnosed easily and conveniently in the familiar Scope interface.
OPC UA can also be integrated into the TwinCAT HMI. This enables the visualization of third-party devices and access to the variables provided there.

The Beckhoff Device Manager can be used to perform device diagnostics with a multitude of system values and is pre-installed in all Beckhoff Industrial PCs as standard. The system values can be accessed via standard functions of the Windows operating system and via special functions of the Beckhoff BIOS. Because the control computer is the central element of the machine control system, any failure can cause high downtime costs. It is therefore essential to be able to check the device. To prevent failure and minimize downtime, it is important to detect critical conditions early on. These include impending heat collapse due to failure of a fan or insufficient passive cooling. For the acquisition, analysis, and evaluation of system data during operation, all Beckhoff IPCs therefore offer the option of sophisticated system diagnostics with standardized, safe access to existing hardware and software components. The Beckhoff Device Manager has an integrated OPC UA Server that is ready to use on every Beckhoff Industrial and Embedded PC and offers access to the diagnostics data of the IPC.

Thanks to TwinCAT's open and flexible communication architecture, the TwinCAT 3 functions are also ideal for implementing retrofit scenarios. An existing machine can be extended very easily via a Beckhoff edge device with OPC UA technology without having to change the machine's program code. When selecting the edge device hardware, the customer can draw on the wide variety of Beckhoff industrial PCs. In principle, every Beckhoff industrial PC is capable of providing and executing such edge device functionalities. This allows you to scale the edge device and the software running on it perfectly for its intended use.

Modularity is an important topic in mechanical and especially plant engineering in order to increase the flexibility and reusability of plant components. This minimizes changeover and setup times. Module Type Package (MTP) has been established as a standard across manufacturers and communicates with OPC UA during productive operation. TwinCAT supports effective plant module creation in the engineering and production phases using the TwinCAT 3 functions TF8400 and TF8401.

In the classic system architecture, I/O devices, e.g. EL terminals, are connected in TwinCAT and processed and switched there accordingly. In this way, the function TF6100 TwinCAT 3 OPC UA can be used to make the I/O devices accessible via OPC UA.
However, the IoT coupler EK9160 also provides a hardware bus coupler that has an OPC UA server interface directly integrated. The connected I/O terminals are automatically detected when the device is started and made available via the OPC UA server. This enables fast and secure connection of I/O data points. The EK9160 can also demonstrate its strengths in retrofit scenarios: Additional sensors can also be added to an existing plant without much effort and made available via the standardized OPC UA interface.
Products
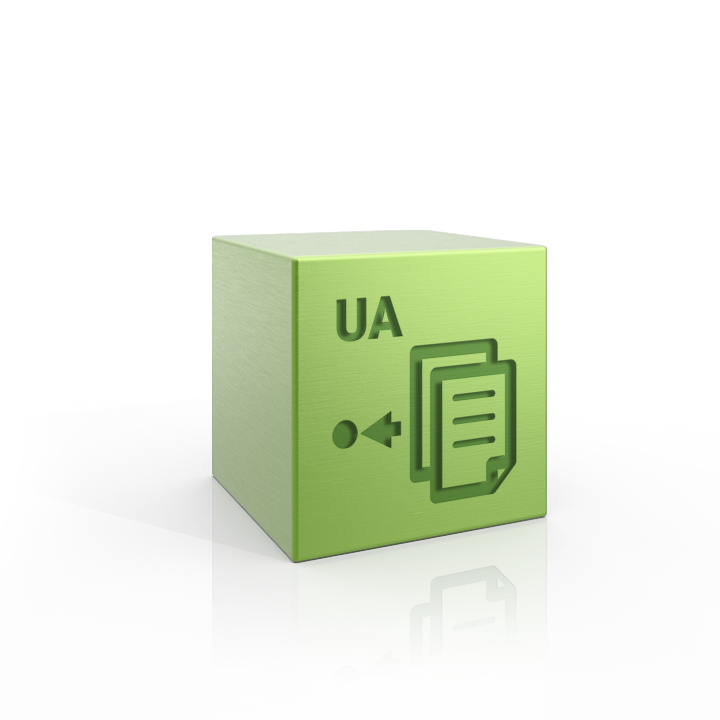
TE6100 | TwinCAT 3 OPC UA Nodeset Editor
The TwinCAT 3 OPC UA Nodeset Editor is a software for displaying, customizing, and creating the XML-based formal description files of OPC UA information models known as nodesets.
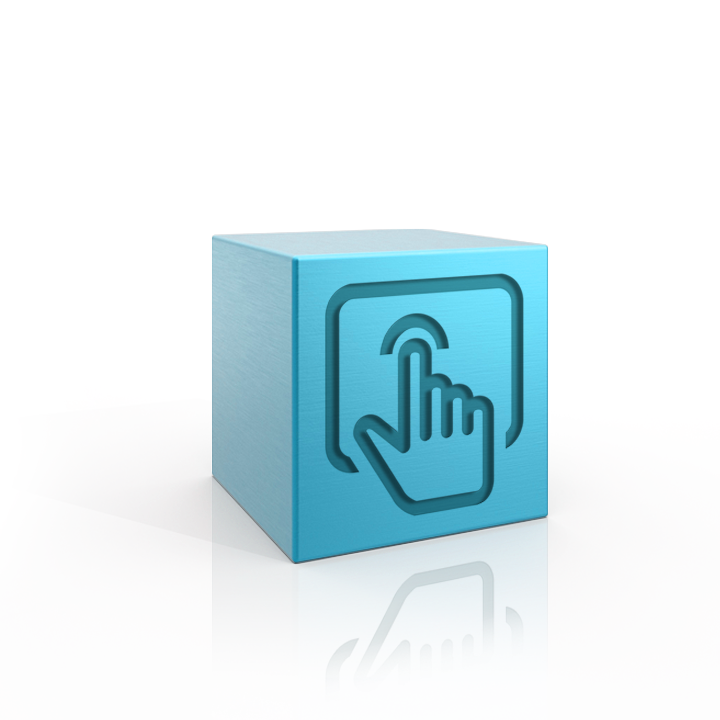
TF2000 | TwinCAT 3 HMI Server
The TwinCAT 3 HMI Server is a modular web server that provides the human-machine interface (HMI). It supports all CPU classes from Arm® to multi-core. The powerful architecture enables a wide range of application scenarios from local panel solutions to multi-client, multi-server and multi-runtime concepts.
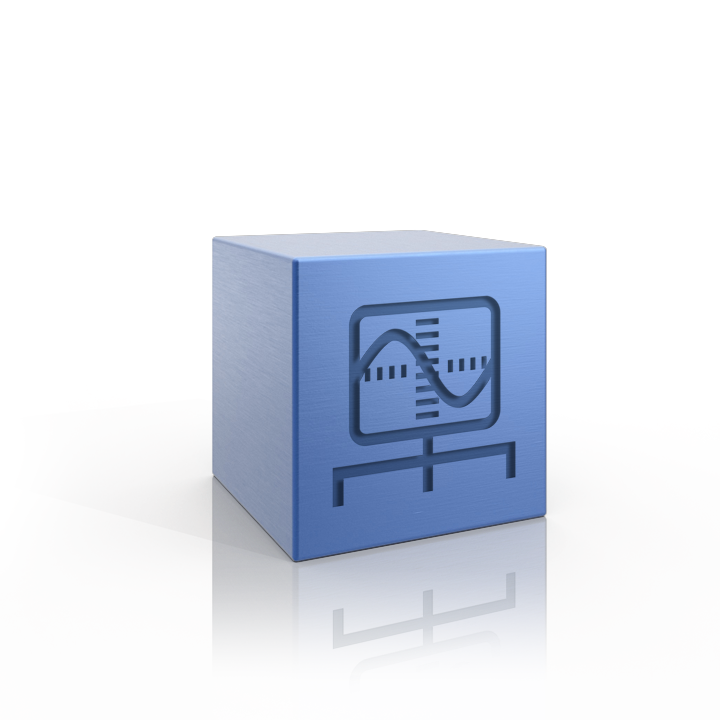
TF3300 | TwinCAT 3 Scope Server
The TwinCAT 3 Scope Server prepares data for the graphical display in the TwinCAT 3 Scope View. It can be used with the Scope View Base or the TE1300 Scope View Professional version. The Scope Server is particularly suitable for autonomous data recording in distributed systems in the production, plant or machine network. It not only has TwinCAT-specific communication interfaces, but also a standardized communication connection via OPC UA.
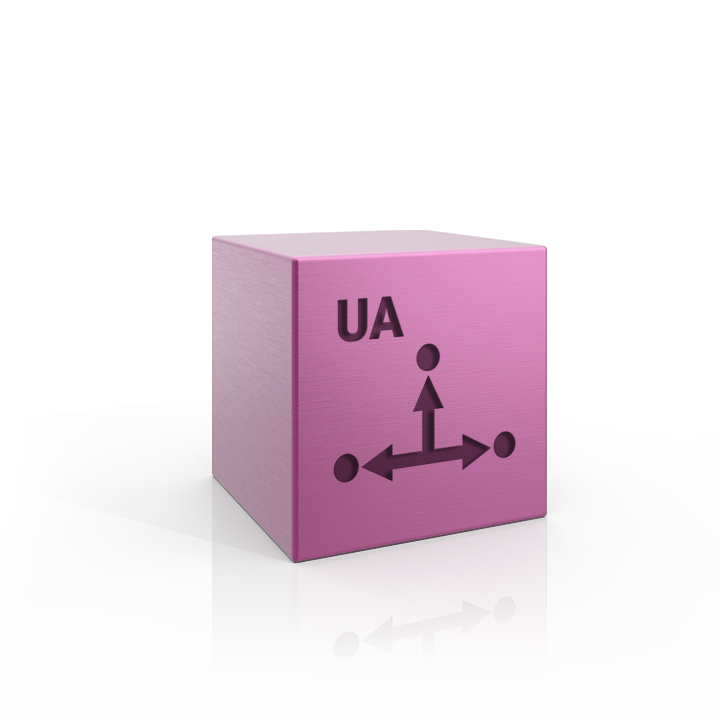
TF6100 | TwinCAT 3 OPC UA
OPC UA is a platform-independent, service-oriented communication architecture for reliable, secure and multisupplier data transport from the production level to the production planning and ERP system or to the cloud.
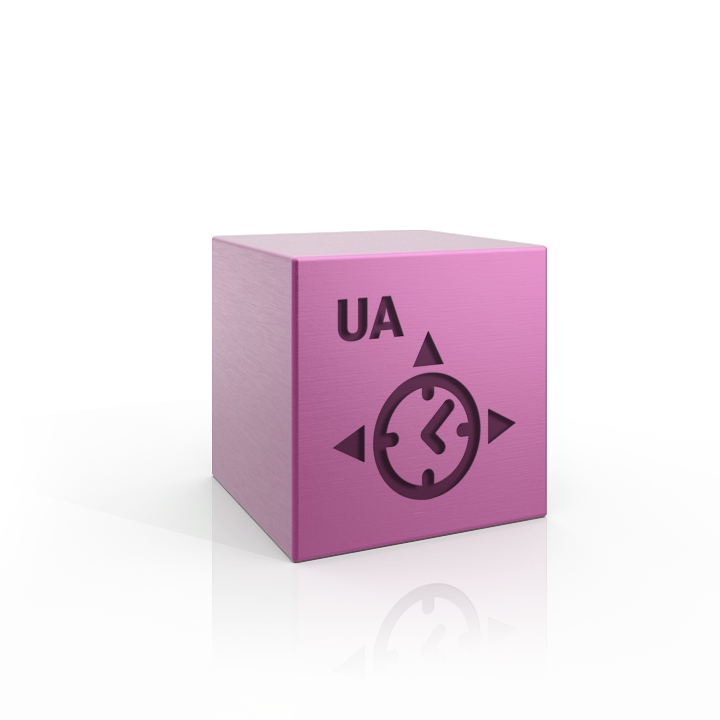
TF6105 | TwinCAT 3 OPC UA Pub/Sub
TwinCAT 3 OPC UA Pub/Sub extends the OPC UA client/server architecture to include publisher/subscriber communication patterns. The TF6105 TwinCAT 3 OPC UA Pub/Sub provides the necessary implementations of the protocol so that these kinds of communication patterns can be readily integrated into the TwinCAT application. It includes various transport protocols as defined in the corresponding OPC UA specification part (OPC10000-14), e.g. UDP and MQTT.

TF6720 | TwinCAT 3 IoT Data Agent
The TwinCAT 3 IoT Data Agent provides bi-directional IoT communication functions in the form of a gateway application that can be configured and operated independently from the TwinCAT real-time environment.
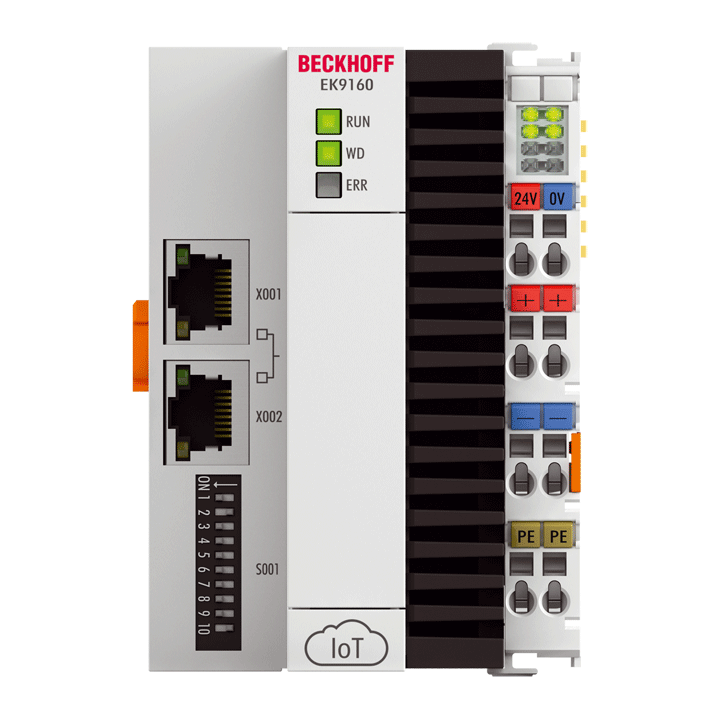
EK9160 | IoT Bus Coupler
The EK9160 Coupler provides direct connectivity for EtherCAT I/Os to the Internet of Things (IoT) without the need for a control program. It converts the E-bus signal representation to different IoT communication protocols and enables in this way the simple and standardized integration of I/O data into cloud-based communication and data services. Neither a controller nor prior programming is necessary. The I/O data transmission can be parameterized in a user-friendly configuration dialog of the integrated web server providing access via any browser. The required cloud services and security functions (authentication, encryption, etc.) can also be conveniently configured using a browser. Following parameterization, the coupler autonomously transmits the digital or analog I/O values to the cloud service, including timestamp.

Ultra-compact Industrial PCs
The scalable C60xx series combines maximum computing power in what is currently the most compact format with a wide range of options for installation in the control cabinet.