

MATLAB® and Simulink® have grown worldwide and become established programming environments for diverse applications, including among budding engineers. There are many reasons for this development. MATLAB® and Simulink® provide solutions that enable a complete focus on the engineering task. This is perfect for didactic concepts in teaching environments and efficient in industrial applications.
Advantages of MATLAB® and Simulink®

- early validation of software functionality through simulation
- virtual commissioning based on physical model
- direct import of CAD models
- development and test of control software and process logic
- analysis of measurement and process data
- interactive apps for the development of algorithms
- train and optimize AI algorithms
- Parallel Computing
From MATLAB® and Simulink® to TwinCAT 3
Using TE1401 TwinCAT 3 Target for MATLAB® and TE1400 TwinCAT 3 Target for Simulink®, it is possible to execute the analyses and simulations developed in the globally used MATLAB® and Simulink® programming languages in TwinCAT runtimes in hard real time. The programming, which was first validated and transferred to the actually connected TwinCAT system landscape, can immediately assume the control and monitoring tasks in the customer applications as a productive code without incurring any risk of unforeseeable errors in the development phase.
Analyses and simulations created in MATLAB® or Simulink® can be connected with the TE1410 TwinCAT 3 Interface for MATLAB® and Simulink® to TwinCAT runtime environments via a high-performance communication interface. The MATLAB® functions or Simulink® models are run in the MATLAB® or Simulink® process, and these processes can exchange data bidirectionally with the TwinCAT runtimes. With TF6701 TwinCAT 3 IoT Communication, the communication functionality can also be transferred to the ThingSpeakTM IoT platform.
MATLAB® and Simulink® customer applications in TwinCAT 3

Test system of a heavy-duty bearing test bench for the main bearing of wind turbines
Using leading automation technology, wind turbines with diameters up to 6 meters can be tested on the world’s most powerful heavy-duty bearing test bench on SKF main bearing. The highly complex control system was developed and tested in MATLAB® and Simulink® and does not need to be re-programmed for the controller. The test bench is a custom-made product, i.e. the control cannot be tested on a prototype. It was possible to meet this challenge thanks to the automatic code generation and integration of the controller developed in MATLAB® and Simulink® in the test control (Rapid Control Prototyping) as well as the virtual commissioning of the controllers based on a model of the machine.
That way risks due to malfunctions during commissioning could be reduced as well as commissioning time and costs.

Yarn and fiber production with the Zero Twist Feeder
The Zero Twist Feeder feeds yarn into the weaving machines without a single rotation. Weaving machines operate at high speeds and pull on the spool at highly irregular intervals. A buffer arm is used to balance between the spool and the gripper. The buffer arm feeds the weaving machines with the exact required amount of yarn at optimum speed for weft insertion. Speeds of up to 850 meters/minute per entry can be achieved during production. The problem that can arise when weaving carbon fibers, glass fibers or plastic strips is the occurrence of twists or loops at these high speeds.
The problem was solved by first creating a digital twin of the machine. The programming of the entire software was done in Simulink®. The model was divided into several partial models that each represented an aspect of the mechanical engineering. Before IRO tested the algorithms on the actual hardware in Sweden, Vintecc conducted extensive virtual simulations in Belgium to ensure the machine worked as designed.
Combining Simulink® with the Beckhoff TwinCAT Technologie via the TwinCAT 3 Target was a great advantage in this application since it requires no PLC code. The model could be directly integrated in detail into TwinCAT. Changes made to the parameters in the model, TwinCAT or the hardware can be immediately transferred.

Magway Transport system – shifting a sophisticated algorithm to the lowest possible level
Magway uses MATLAB® and Simulink® for the implementation of an encoder-less control of linear synchronous motors that allow for an autonomous, sustainable package delivery through subsurface tubes.
Using the TwinCAT Target for Simulink®, control algorithms are implemented directly on an industrialized platform, and do so with fewer components, decentralization, higher system availability and shorter development cycles. This way the development cycles are shortened thanks to the in-loop debugging. The core IP was developed in MATLAB® and Simulink®. By using this software directly instead of through an inconvenient port, Magway always has the right tool for the right job.

Control software for 6 MW offshore wind turbines
Offshore wind turbines must ensure high availability levels with low maintenance requirements. The operation of this facility must be predictable and safe to control at all times. It is hardly possible to test the highly sensitive control software under real conditions.
By using the concept of the model-based design with Simulink® and TwinCAT, each function of the system can be developed, tested and verified. The safe and reliable control software can also be developed faster and more cost-effectively. This is possible because the easy integration of the Target for Simulink® in the model-based design process ensures the efficient generation and testing of productive codes on an industrial platform. Furthermore, the communication capabilities of the interface for MATLAB® and Simulink® provide all the tools required for the comprehensive software-in-the-loop testing after the implementation of the code on the Beckhoff controller.
At the same time, the functions of the TE1400 and TE1410 not only resulted in a successful application of the main control software designed in Simulink® for the 6-MW prototype facility but also for each large-scale production after the prototype.

Simutopia is a software and engineering consulting company specializing in model-based design. Simutopia has deep experience in architecting machine models that can be used for design analysis, controls deployment, real-time simulation, and testing. Expert knowledge is used to leverage the combined power of MathWorks® and Beckhoff software tools for rapidly deploying and iterating advanced control algorithms on the TwinCAT platform. Simutopia is a member of the Beckhoff Integrator Group (BIG).
Developing robotic systems control algorithms includes creating kinematics and dynamics models of the robot mechanisms. These models can be quite complex based on the robot topology and number of degrees of freedom. To provide efficient and cost-effective solutions to their clients, Simutopia developed a custom application in MATLAB®, called NewtonsLab, to create these models easily using SimscapeTM MultibodyTM. TwinCAT 3 Target for MATLAB® and TwinCAT 3 Target for Simulink® are used to automatically deploy these models on TwinCAT for real-time control directly from NewtonsLab. Furthermore, the TwinCAT Interface for MATLAB® and Simulink® enables to live-stream data between TwinCAT and NewtonsLab via ADS. This helps to quickly change controller parameters and validate the deployed code on TwinCAT by comparing the performance of the virtual machine with that of the real hardware based on the same inputs. This is tremendously helpful to rapidly prototype and test the control algorithms.
If you also have similar examples of applications and questions about the integration of your MATLAB® and Simulink® projects in a TwinCAT software environment, please contact your sales representative or use the Sales contact form.
Products
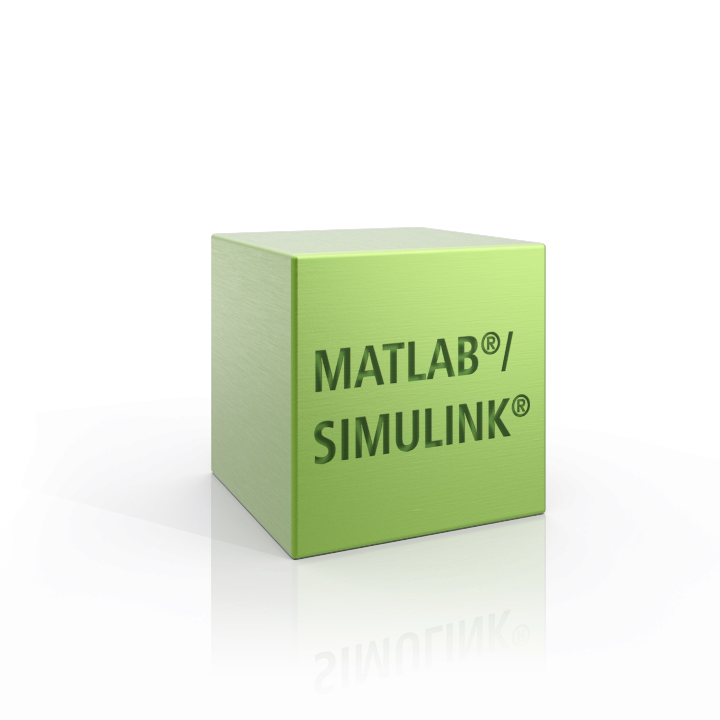
TE1400 | TwinCAT 3 Target for Simulink®
TwinCAT 3 Target for Simulink® provides an interface between Simulink® and TwinCAT. The Simulink® software is developed and distributed by the MathWorks company. The programming environment is based on MATLAB® and is widely used both in science and in industry. Simulink® is a graphic programming environment that is ideally suited to the model-based development process. Simulation models of systems can be created and, for example, control and feedback control algorithms in order to test the models created.
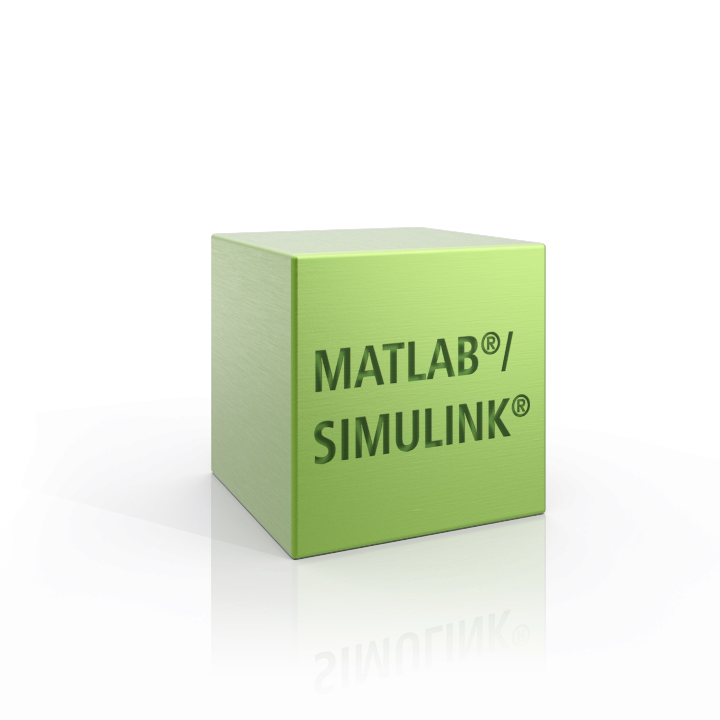
TE1401 | TwinCAT 3 Target for MATLAB®
TwinCAT 3 Target for MATLAB® provides an interface between MATLAB® and TwinCAT. MATLAB®, the language of technical computing, is developed and distributed by the MathWorks company. The programming environment is widely used both in science and in industry. MATLAB® is a script language that is ideally suited for the development of algorithms and mathematical models.
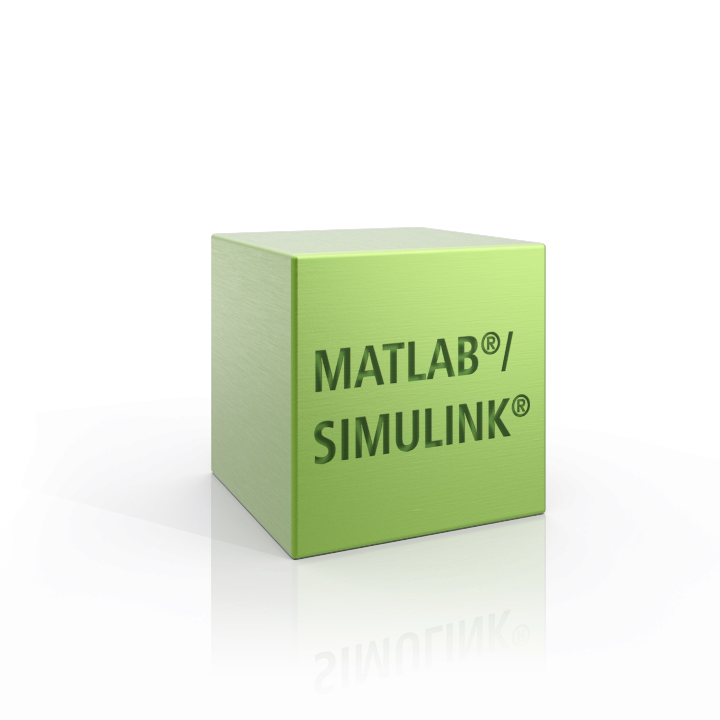
TE1402 | TwinCAT 3 Target for Embedded Coder®
The TE1402 TwinCAT 3 Target for Embedded Coder® is an extension of the TE1400 TwinCAT 3 Target for Simulink®. Building on the existing capabilities of the TwinCAT 3 Target for Simulink®, which uses the Simulink® Coder™ (GRT target) from MathWorks for automatic code generation, the TE1402 also makes it possible to use the Embedded Coder® (ERT target) from MathWorks. The TE1402 essentially leverages the functions of the TE1400 while also harnessing the properties of the Embedded Coder® to achieve target platform specialization. For example, CPU-specific command extensions can be used to make models created on the Beckhoff Industrial PC run faster.
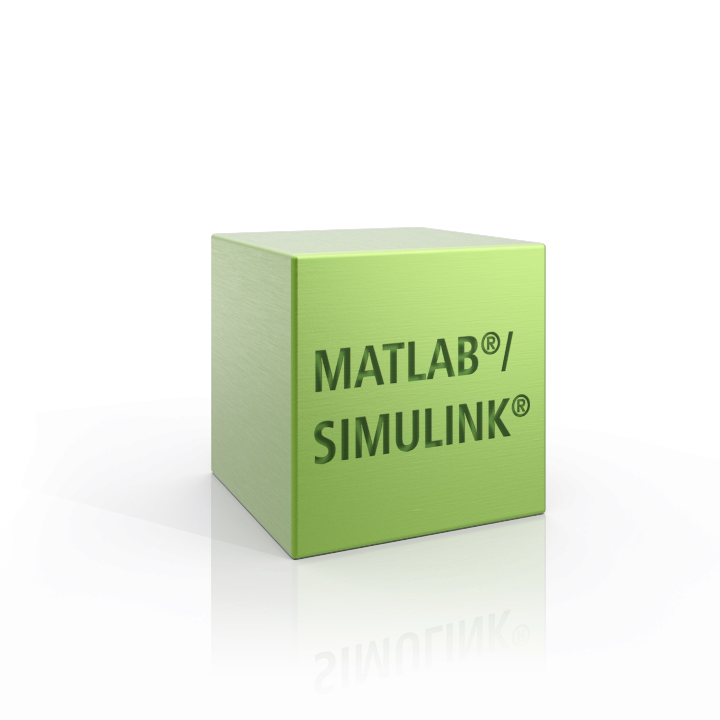
TE1410 | TwinCAT 3 Interface for MATLAB® and Simulink®
MATLAB® and Simulink® are developed and distributed by the MathWorks company. The two programming environments are widely used both in science and in industry. Simulink® is a graphic programming environment that is ideally suited to the model-based development process. MATLAB® is a script language for the development of algorithms and mathematical models.

TF6701 | TwinCAT 3 IoT Communication (MQTT)
TwinCAT 3 IoT Communication provides basic functionalities in the form of PLC libraries for sending and receiving data via the so-called MQ Telemetry Transport (MQTT) protocol.